水泥窑协同处置垃圾现状及技术要点
来源:徐荣 日期:2024-03-13 访问量:3514 次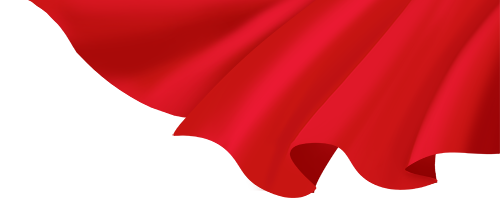
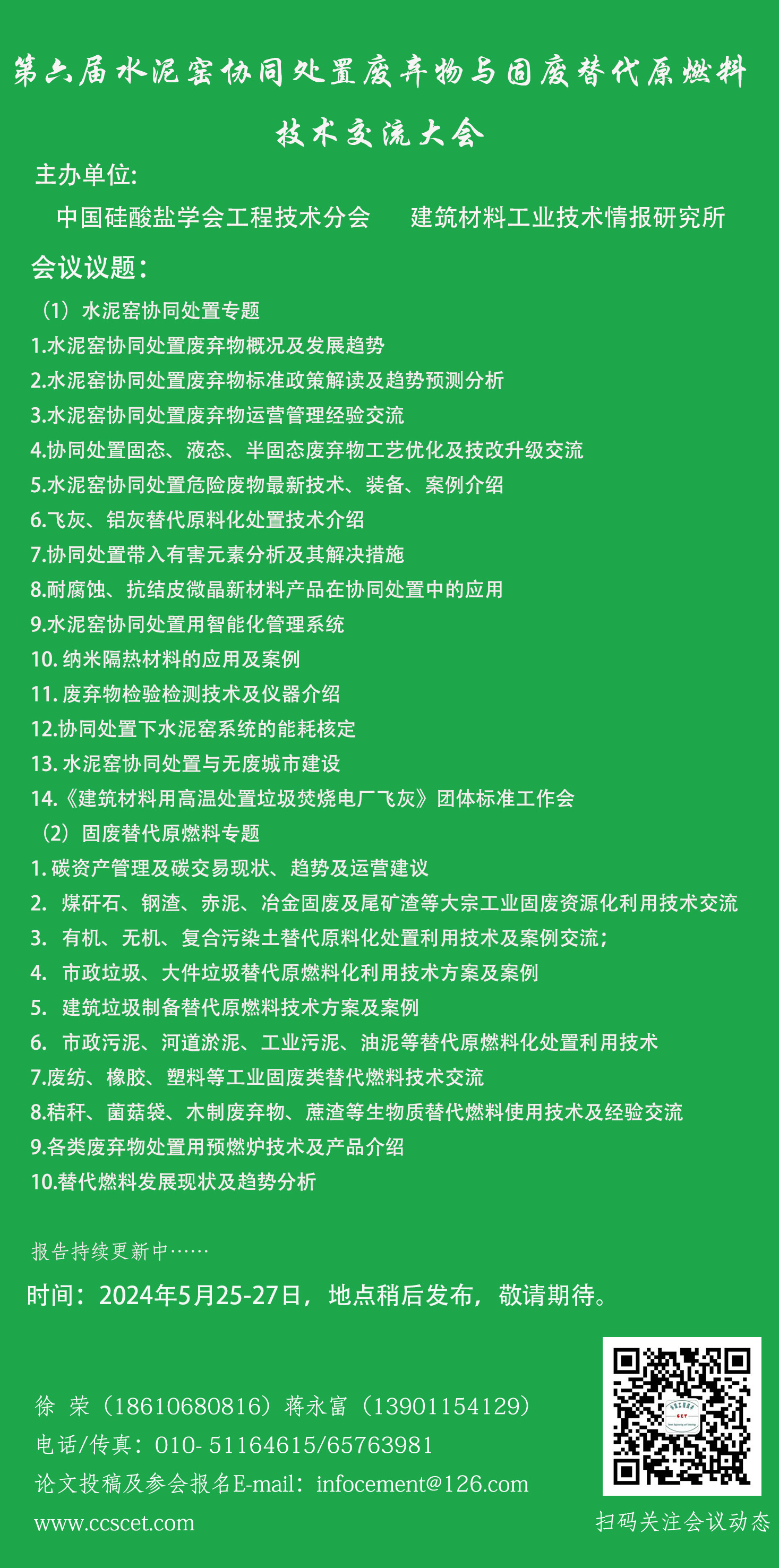
1.7天堆存发酵+破碎筛分+燃烧器入分解炉;
2.破碎筛分+挤压脱水(或有)+不可燃物入生料磨+可燃物直投分解炉+渗滤液入窑;
3.破碎筛分+挤压脱水(或有)+预燃炉(气化炉、热盘炉、阶梯炉、流化床炉)
总体来说,水泥窑协同处置市政垃圾处置量大,实现了市政垃圾无害化、替代原燃料化处置利用,是市政垃圾处置的最佳技术路线。相较于市政垃圾焚烧发电,水泥窑协同处置生活垃圾无需热能-蒸汽-电能能源转换,能源利用效率更高;不产生灰渣及飞灰等危固废,资源化更加彻底。但受制于目前垃圾处置补贴费用补贴到发电上而非直接补贴到垃圾处置上,一定程度上抵消了该技术相较于垃圾焚烧发电的优势。
为消除上述劣势,目前国内已有水泥企业按照垃圾焚烧发电的思路,拿到电网上网许可,利用已有余热发电设施,在厂区内进行垃圾焚烧发电并对底渣、飞灰、尾气进行协同处置。无害化、替代原燃料化处置生活垃圾的同时,实现厂区零购电并外送电能,实现效益最大化。

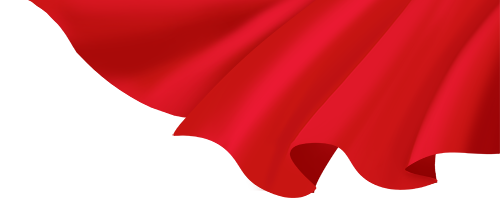
由此可见,水泥窑协同处置生活垃圾对水泥企业节能减排、绿色转型发展意义重大。在水泥行业即将纳入碳交易市场的背景下,更值得大家关注。
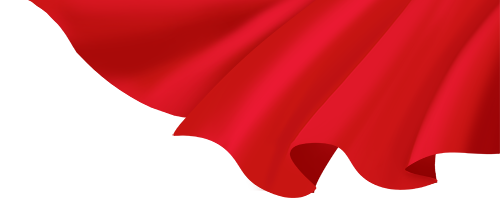
处置过程中应尽量降低入窑垃圾水分,水分入窑后会增加无用能耗并增大烟气量,进而对熟料产量造成影响。据专家估算,每入窑1吨水会降低2吨熟料产量。
2.烟气量与阻力
生活垃圾热值低、水分高、燃烧特性差,每燃烧1公斤生活垃圾所需空气量约1.4标立,比等量的煤多0.4标立左右。1公斤垃圾燃烧新产生烟气约1标立,1公斤煤燃烧新产生烟气约1.3标立。处置生活垃圾系统烟气量会显著增加约10%,预热器阻力会相应增大。因此在处置生活垃圾后,企业须在降阻改造、降低产量、降低垃圾处置量方面寻找最佳平衡点。以最合适的燃料替代率获取最大的效益。
3.氯元素
原生垃圾氯元素含量约1%,若1条水泥生产线日处置500吨生活垃圾,则入窑氯元素约5吨/天。氯元素的循环富集会导致生产线结皮堵塞、设备腐蚀、氯化氢排放超标等问题出现,影响熟料产质量、生产安全及环保达标。同时,水泥国标氯离子限值为0.06%,进一步限制了入窑氯元素的量。为解决上述问题,企业需要通过配套相应的除氯设施并对高氯窑灰进行相应的预处理进而资源化利用来解决。
4.环保排放
处置生活垃圾会导致氯化氢排放明显升高。国标要求窑尾烟囱氯化氢低于10毫克/立方米,实际生产中有的协同处置生活垃圾企业会达到70毫克/立方米。这可以通过生料磨与窑同时启停来对烟气中的氯化氢进行吸收来解决。
协同处置生活垃圾的燃尽率不高会导致系统一氧化碳排放严重超标。虽然目前对协同处置生活垃圾水泥企业一氧化碳排放没有限值考核,但一氧化碳会浪费大量能源,并影响水泥产质量。企业在生产过程中需通过合理的预处理措施提升垃圾品质,技改升级改善垃圾燃烧条件来解决。